You are interested in our material tests?
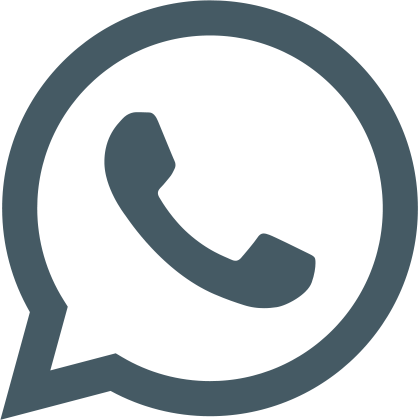
info@qitech.de
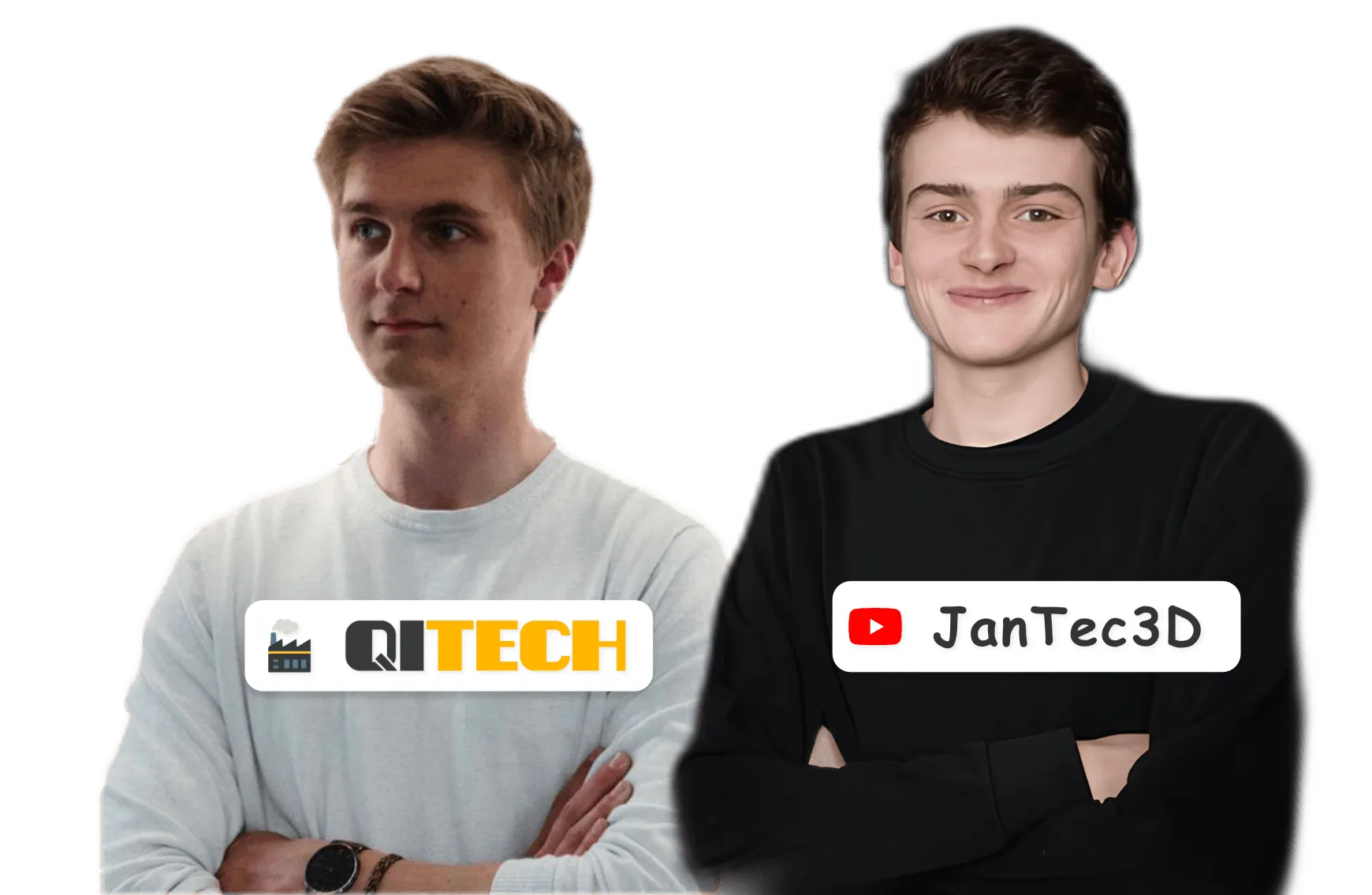
Request a quote for a material test
Jan and Milan first met back when they were in school.
While Milan was building QiTech, Jan started his own YouTube channel about 3D printing.
With our materials research, we create the condition for easy, efficient & cost-effective recycling.
Grinding, Drying, Filament Extrusion, 3D Printing & Filament Properties - We test the entire process of filament production with our JARVIS machines.
This way, our customers can make data-based decisions on how to integrate circular economy within their own operations.
What is the amount of filament that could be produced per hour? (Kg/h)
What would be the properties of the filament?
(Tensile test, temperature test, notched bar impact test, 3-point bending test)
Which nozzle diameter works best?
How much should you cool the filament after extrusion?
On which printers can you print the finished filament?
Detailed PDF report with photos & videos!
Can it be processed into filament?
How to shred the material? Which shredder would we recommend?
Which throughput is achievable within a potential filament production?
What does the granulate look like?
Should the material be dried? If so, how long / at what temperature?
From a student start-up in a garage to an international engineering company.
We have developed modular machines that allow you to make your own filament (effectively the ink for 3D printers) from different materials. We sell the recycled filament and our JARVIS machine systems to companies and research institutions worldwide.
In addition, we are continuously researching recycling methods and share our know-how publicly with the community.
Jan Wegener is a passionate maker and expert in the field of 3D printing. Back in his college days, he started his ownYouTube channel where he showcases various 3D printers and performs filament analysis.
He gained his expertise in creating test series and test equipment during an internship at Germany's largest 3D printing YouTuber "CNC Kitchen".
Jan Wegener strives to break new innovative ground in the field of additive manufacturing.
First part - QiTech
Drying makes the difference whether you are successful or not in filament extrusion - That's why we've even dedicated a few videos and how-to' s to this topic on our Academy section. With the Digicolour high-tech dryer we not only have constant drying, but also full digital data recording so we can determine the perfect drying time, temperature and dew point.
With the JARVIS Shredder & JARVIS Pro Shredder we have two powerful mills for high quality & uniform granules on site. The current measurement enables an evaluation of both energy and costs to be made at the end of the test series.
In our JARVIS Extruder we have combined all our experience in plastics processing of the last years. Special features are especially the pressure sensor and the cloud connection, through which we can display all temperatures as a history and export them as .csv for the report - This allows us to provide even better evaluations and results.
The JARVIS Airpath is our easy-to-use cooling unit that ensures an even temperature of the filament for spooling. This temperature is very important: filament that is too hot can stick together on the spool and filament that is too cold may not bend enough to fit tightly.
The JARVIS DRE is our solution for monitoring the filament diameter during production. Through our software, we can display the values of the diameter as a history and export it as .csv for the report.
The most important parameter for perfect filament is the pull-off speed. We find the maximum production speed that is achievable, while still maintaining a good quality. In addition, upon request, we can test the spools that you plan to use later on with our JARVIS Winder.
Second part - JanTec
In order to determine the extent to which the components made from the recycled materials can later be subjected to loads and what influence the recycling process has on the mechanical properties, various tests were carried out under constant conditions.
On request, we can also carry out more in-depth tests in individual fields.
Tensile test
A tensile test can be used to investigate the strength of plastics. It is crucial for evaluating the performance of plastics in applications that are subjected to tensile loads.
For this purpose, a manual crank test rig was equipped with a load cell to enable the tensile force applied to the specimen to be measured in Newtons. The measurement is made using an HX711 signal amplifier. The measured tensile force versus time is recorded. At the high point of this curve, the maximum tensile force until breakage can be read.
Divided by the fracture area of the specimen used, the tensile strength in MPa is obtained. We perform the test in XY and Z direction.
Tensile strength
A notched impact test is used to evaluate the toughness and impact strength of a material. For this purpose, a notched specimen is cut with a sudden impact load.
In the setup used, a hammer oscillates, smashing the clamped specimen. This absorbs some of the potential energy of the hammer.
The energy that can be calculated from this, divided by the fracture area of the specimen, gives the impact strength in MPa.
3 point bend test
A 3-point bending test can be used to investigate the stiffness, in other words the resistance to loads, of the materials. The comparable value here is the flexural modulus in MPa. The higher this value, the lower the deformability.
Temperature test
Since the plastics used are thermoplastics, they start to soften at higher temperatures until they eventually melt - as they do during 3D printing and recycling.
Especially for components that are used in warmer environments, such as outdoors or near electronic components, it is important to know at what temperature they can soften and change shape.
What you get in the end
We provide all the data to decide:
Does it make sense to process this plastic into filament and run it in a closed-loop process
Featured Posts